Identify welding gauge type
using AI
Below is a free classifier to identify welding gauge type. Just upload your image, and our AI will predict the type of welding gauge being used - in just seconds.
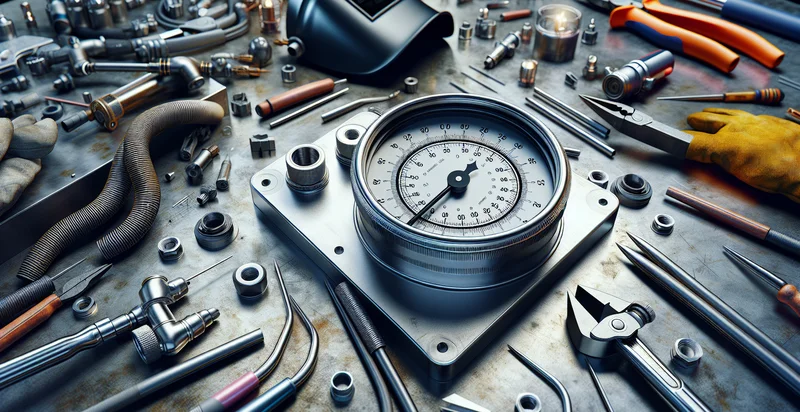
Contact us for API access
Or, use Nyckel to build highly-accurate custom classifiers in just minutes. No PhD required.
Get started
import nyckel
credentials = nyckel.Credentials("YOUR_CLIENT_ID", "YOUR_CLIENT_SECRET")
nyckel.invoke("welding-gauge-type", "your_image_url", credentials)
fetch('https://www.nyckel.com/v1/functions/welding-gauge-type/invoke', {
method: 'POST',
headers: {
'Authorization': 'Bearer ' + 'YOUR_BEARER_TOKEN',
'Content-Type': 'application/json',
},
body: JSON.stringify(
{"data": "your_image_url"}
)
})
.then(response => response.json())
.then(data => console.log(data));
curl -X POST \
-H "Content-Type: application/json" \
-H "Authorization: Bearer YOUR_BEARER_TOKEN" \
-d '{"data": "your_image_url"}' \
https://www.nyckel.com/v1/functions/welding-gauge-type/invoke
How this classifier works
To start, upload your image. Our AI tool will then predict the type of welding gauge being used.
This pretrained image model uses a Nyckel-created dataset and has 19 labels, including Backing Bar, Bevel, Butt, Cap, Corner, Edge, Face, Fillet, Groove and Keyhole.
We'll also show a confidence score (the higher the number, the more confident the AI model is around the type of welding gauge being used).
Whether you're just curious or building welding gauge type detection into your application, we hope our classifier proves helpful.
Related Classifiers
Need to identify welding gauge type at scale?
Get API or Zapier access to this classifier for free. It's perfect for:
- Quality Control in Manufacturing: The welding gauge type identifier can be used in manufacturing facilities to ensure that the correct welding gauges are utilized during production processes. By integrating this function into quality assurance systems, manufacturers can automate the detection of incorrect gauge usage, leading to higher quality products and reduced rework rates.
- Compliance Verification: In industries with stringent safety regulations, such as construction and aerospace, the welding gauge type identifier can assist in compliance monitoring. This function can automatically verify that the appropriate welding gauges are being used according to specific industry standards, minimizing the risk of violations and enhancing operational safety.
- Training and Education: Educational institutions and training programs in welding can utilize the identifier to teach students about different types of welding gauges. This tool can provide real-time feedback during training sessions, helping learners understand the implications of using the correct welding gauge, ultimately enhancing their practical skills.
- Inventory Management: Businesses can implement the welding gauge type identifier in their inventory management systems to track the availability and usage of various welding gauges. By accurately identifying gauge types, organizations can streamline inventory levels, reduce waste, and ensure that the right tools are available for projects.
- Maintenance Scheduling: The welding gauge type identifier can play a crucial role in maintenance programs by determining the types of gauges being used in different applications. This information can help schedule maintenance activities more effectively, ensuring that the correct gauges are maintained and reducing downtime caused by equipment failure.
- Supply Chain Optimization: Manufacturers can leverage the welding gauge type identifier to optimize their supply chain by ensuring that suppliers deliver the correct types of gauges. This function can reduce the risk of overstocking or understocking incorrect gauges, leading to more efficient procurement processes and lower operational costs.
- Process Automation: Integrating the welding gauge type identifier with robotic welding systems can enhance automation efforts. By enabling machines to recognize and adjust settings based on the welding gauge type, businesses can achieve more precise welding outcomes and increase productivity while reducing human error.